CASWELL COUNTY, NC, July 2008 — As soon as the technicians hooked up his solar collectors, Chris Clemens noticed that the panels weren’t collecting enough sunlight to produce the amount of energy he wanted. Two weeks later, a gust of wind blew the collectors out of alignment with the sun. And two weeks after that, electronic components began to rust and then fail completely.
It wasn’t the best month for MegaWatt Solar, a company that Clemens had started with fellow physicist Chuck Evans and computer scientist Russ Taylor. Sure, they’d known that something would go wrong. After all, they hadn’t just plopped solar panels on a rooftop; they had built a new kind of solar collector that tracks the sun across the sky and pumps energy onto the power grid. The sixteen units in Caswell County were the first ones they’d deployed in the field. Still, they hadn’t thought that the problems would be so big or surface so fast.
By July 2008, Clemens, Evans, and Taylor had been living and breathing MegaWatt Solar for nearly three years, taking no vacations and using all the skills they had to build a better kind of solar collector. They weren’t about to give up.
“Everyone we hire gets a little speech,” Clemens says. “Not about being philosophically ‘green’ but about changing the way we make energy for everybody. It’s about the fact that we’re going to be looking at each other in the dark in fifty years, huddled around fires, if we don’t get off our butts and do something about this country’s energy problem.”
The malfunctions at the Caswell power plant weren’t insurmountable, but the solutions had to come fast. The company was running low on money. And the solutions had to be cheap, or else Clemens, Evans, and Taylor would fall short of their goal: to produce solar energy at a price that beats coal, oil, natural gas, and nuclear power. They knew that this was possible.
“If this works, and I think it will, then it won’t be long before you see these kinds of solar arrays popping up all over the place,” Clemens says. “It will be like satellite dishes for television. One day there were none; the next day, they were everywhere.”
PASCAGOULA, MS, August 30, 2005 — Chris Clemens had never been interested in solar power before Hurricane Katrina slammed into his hometown and wreaked havoc on the lives of his friends and family. He delivered supplies twice to the Gulf Coast, the second time with Dan Gregory, an energy analyst Clemens didn’t know but who had volunteered his truck and time.
The storm had not only wiped out oil refineries but also destroyed parts of the nation’s power grid — transmission and distribution lines. Gregory, it turned out, had been thinking about the fragility of the power grid for a long time. He knew that the grid was vulnerable to brownouts and blackouts, even without a storm. He knew that the grid wasn’t good at dealing with changing levels of demand for electricity. And he knew that utility companies struggled to pump different kinds of renewable energy onto the grid. That’s one of several reasons why power companies have been reluctant to embrace alternative forms of energy.
On that trip to the Gulf Coast, Gregory had the idea that scientists from different fields would have unique perspectives on alternative energy. He asked Clemens to start a consulting company with two or three other UNC professors interested in energy issues. Then, with Gregory, they’d work with utility companies to solve energy problems.
Clemens approached his friend Chuck Evans, a theoretical physicist with a love for building things. Evans had been studying the concept of peak oil — the hypothetical point in time when oil cannot be extracted from the ground any faster, resulting in decreased production and, eventually, decreased supply. When this will happen is up for speculation. Some people, including Evans, think that it already has happened. Clemens didn’t need to persuade Evans to study energy issues.
Clemens then called Russ Taylor, who has made it part of his mission at UNC to team up with researchers from different fields. Taylor loves solving problems, especially when he can use new codes, algorithms, and models.
Still, they weren’t consultants; they were professors. Clemens told them, “We need a history, a problem that we’ve solved to show people how we think.”
They began studying alternative fuels that might help ease the pain of oil depletion. They looked at solar power, and although so many people had already worked on it, Clemens and Evans saw a lot of room for innovations. “We started thinking about how we could make the price of solar energy drop way down to coal’s level,” Evans says. They knew that any solution would have to include much less silicon than typical solar panels use. Silicon is too expensive. Any new solar collector had to be cheaper than dirt or else power companies wouldn’t care.
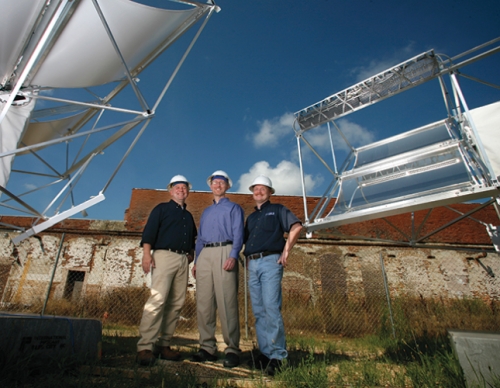
Photo by Coke Whitworth. ©2009 Endeavors magazine.
From left, physicists Chris Clemens and Chuck Evans and computer scientist Russ Taylor wanted to help solve our power-grid problems. They wound up creating a solar-energy company.
Click to read photo caption. Photo by Coke Whitworth. ©2009 Endeavors magazine.
They found that other researchers had come up with ways to concentrate sunlight. Clemens and Evans thought that they could use some kind of cheap mirror to concentrate the sun’s rays and then reflect a very bright band of light onto a narrow set of solar cells. This kind of solar receiver would be much smaller than the large rooftop panels. It would use much less silicon, which means that it would be much cheaper but still create the same amount of electricity. And if they could make a collector that mechanically tracked the sun across the sky, they’d get even more bang for their buck.
Tracking the sun didn’t seem like a problem. Clemens had twenty years of experience as an astrophysicist tracking objects in the night sky, and he and Evans had helped build UNC’s SOAR telescope in Chile. (See Endeavors, Fall 2004, “Star Power.”)
They met with Dan Gregory, who loved their idea because the unit they described would be mostly infrastructure — metal and mirrors. It would last a long time, as long as a coal plant, with minimal upkeep. It would use much less silicon than conventional solar panels. And when the silicon cells needed upgrading, they could easily be replaced without scrapping the entire unit.
Gregory thought that utility companies would be interested, especially if the power plant came equipped with low-cost inverters to convert direct current from the solar collectors into alternating current, which is what utility companies use.
And Gregory saw a major role for himself. His company, Plymouth Systems, Inc. in Chapel Hill, could build control systems to monitor the solar-power plant’s performance, detect power failures, and perform off-site diagnostic tests through a secure website. Also, this solar-power plant could be tied to the grid at landfills where some communities already recover methane to pump electricity onto the grid. Wind, methane, and solar technologies could be tied to one system that Gregory knew how to manage.
Another fact excited all four men: no other solar-power company was making the control systems and inverters that utility companies needed.
Clemens, Evans, Taylor, and Gregory met with engineers and top executives at a large utility company in North Carolina. The company liked the idea and even considered investing money in the project. “But they told us we needed to become a real company and find a lead investor,” Clemens says.
And there was another small matter: they still had to build the solar collector and make the thing work.
CHAPEL HILL, NC, Fall 2005 — First, the team had to make a concave reflective surface that would focus light into a narrow band. Clemens thought that expandable foam would work — think fake wood, not Styrofoam. “It’s cheap,” Clemens says. “And I knew it would be strong enough.”
Evans was skeptical. They’d have to make a mold in order to shape the foam. Clemens started searching online and found lots of possibilities, some of them not so cheap.
“At this point, we were funding everything ourselves,” Evans says. “When it comes to convincing your wife that you need to take money out of the bank, well, that kind of narrows your choices a little bit.”
Clemens found an inexpensive material called Dibond that’s used to make advertising signboards — think, Waffle House, next exit. He thought he could tease the Dibond into the proper shape for a mold. He ordered some and then drove to Raleigh with Evans. They strapped the four-by-ten-foot piece of Dibond to the top of a pick-up truck and drove very slowly back to Chapel Hill.
During a brainstorming session, they realized that they wouldn’t need to make a mold if the Dibond itself could serve as the mirror. The Dibond seemed perfectly malleable but wasn’t very shiny. Evans, though, knew of a reflective material that lines the insides of tubular skylights. “We thought maybe we could cut open those tubes, unroll them, and laminate them onto our Dibond,” Evans says. They bought some tubes.
Then they found a company that makes aluminum parts to spec. “You pay online and they ship it to your door,” Evans says. “We opened the box and had hardware to start putting this thing together like an Erector Set.”
That spring of 2006, they struck up a friendship with a scientist at BP Solar, who sent samples of BP’s special silicon cells suitable for concentrated sunlight. Then, while assembling the collector at Evans’house, they attached the cells to their receiver — just a flat piece of aluminum about four feet long. Evans laminated the tubular reflective surface onto the Dibond panel, which they flexed into a concave shape. They secured the mirror in place with metal brackets and then attached the solar-cell receiver.
It took a few hours to assemble. Then, since it was still sunny, they recruited Evans’ teenage sons to haul the four-by-ten-foot solar collector from the back deck to the front yard. They torqued the aluminum frame so that the mirror could focus a band of light onto the narrow strip of silicon. And there it sat, collecting sunlight. Then they used jumper cables to take the energy off the receiver. Current was charging through it. They had their proof of concept.
“That was a lot of fun,” Evans says. “I remember we had to go get sunglasses because that band of light was really bright. But we were all proudly beaming. Excuse the pun.”
Clemens says he allowed himself a second of celebration before thinking of the next step. “This whole thing is a like a series of battles in a war,” he says, “and we had just cleared a checkpoint.”
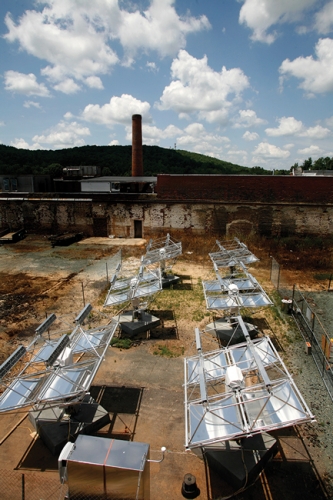
Photo by Coke Whitworth. ©2009 Endeavors magazine.
Outside old Dimmock’s Mill in Hillsborough, North Carolina, six solar trees track the sun to pump energy onto Orange County’s power grid. UNC researchers designed the units to be cheap and effective alternatives to fossil fuels and existing rooftop solar panels.
Click to read photo caption. Photo by Coke Whitworth. ©2009 Endeavors magazine.
By this time, Clemens, Evans, Taylor, and Gregory had created MegaWatt Solar and named Gregory CEO. In December of 2006, still on their own dime, they moved MegaWatt Solar into an old mill building in Hillsborough, North Carolina. Four months later — still teaching full-time and running their labs at UNC — they got a major boost when two solar companies in Norway agreed to pump venture capital into MegaWatt Solar. Gregory immediately handpicked a marketing expert and a systems operations manager. The company hired local electricians and a few Carolina and NC State graduates.
Clemens, who is more comfortable building things than theorizing about them, set out to design the double-axis drive — the motors that would allow the collectors to track the sun. Evans headed the production of the mirrors. Taylor was in charge of creating the computer systems, and his team also wrote software to make the unit track the sun. Clemens and Evans worked on the solar receiver — the narrow aluminum part with small silicon cells.
Most silicon cells are five inches by five inches. For MegaWatt’s purposes, they’re too big and don’t produce the right voltage or number of amps. So Clemens and Evans used a laser to cut the cells down to size and stack them in a series. These cells produced the proper voltage and number of amps, but they still generated too much heat. A fan would help cool the receiver, but fans break and are often too expensive. So Evans and his team designed a heat sink, a series of flat aluminum prongs that absorb heat and allow it to escape through the back of the receiver.
In July 2007, MegaWatt Solar constructed a unit — they called it a solar tree — on a grassy hill next to the company’s facility. The tree had only four mirrors and four receivers. At first, Taylor used a joystick to test Clemens’drive unit. It moved smoothly and didn’t budge in the wind. Then, to make the unit track the sun on its own, they used sensors to measure the voltage that each receiver was generating. By this measurement, the sensors determined whether the mirrors were aimed at the sun. But when clouds rolled by, the mirrors still needed to track the sun. Adam Crain, a former physics major at UNC, wrote an algorithm to make the solar tree follow the sun by counting motor steps. At the end of the day the solar tree clicks back to its dawn position. It’s a solid, patent-pending model that each unit still uses.
But Clemens pointed out that the units didn’t really know where they were aimed. “If a unit blew off course, it would keep counting as though nothing had changed.” It took a long time for the sensors to find the sun again. “It was clear to me that we were missing a piece of technology,” he says.
Meanwhile, Gregory signed a contract to build a solar-power plant for Piedmont Electric Membership Corporation in Caswell County, north of Hillsborough. This plant would have sixteen solar trees, each with sixteen solar collectors. MegaWatt’s twenty employees built the units as fast as they could, but there was no time to test the technology in an environmental chamber, and the company didn’t have ninety thousand dollars to buy one.
“Our thought was, ‘We’ll put the units out there and see how they function,’” Clemens says. “That’s kind of cheeky. But we had a set of milestones we needed to meet to continue our funding.”
MegaWatt Solar hired FLS Energy, a North Carolina solar company, to install the units in the spring and summer of 2008. As soon as FLS technicians assembled the trusses — the big metal frames that support the mirrors — they knew that MegaWatt should’ve assembled the trusses in the factory to ensure consistent assembly. And right away, Clemens saw a problem. On some of the receivers, the bands of light were too wide, which meant that those units would not produce enough energy. The mirrors were permanent parts of the trusses, so there was no way to make adjustments on-site.
These solar trees worked — just not as efficiently as the team had hoped. Some of the other collectors focused perfectly. All of them, though, were affected by the wind. MegaWatt hadn’t done any wind-tunnel tests — again, no time or money — and the trusses couldn’t handle strong gusts. The trees only tracked the sun properly in winds less than fifteen miles per hour.
Then there was the rust. The narrow solar receivers were composed of three panels that were tied together with tiny circuit boards so that electrical current could flow between the panels and then into wires and onto the grid. The circuit boards weren’t sealed well enough. Moisture seeped in. Within a month they corroded and the units started to fail.
In the backs of their minds, Clemens and Evans knew that problems like these might happen. They were scientists, after all, and scientists depend on failure to learn. So Clemens saw no reason to panic.
“Our whole approach has been to see the entire system at once to see its functionality,” Clemens says. “Not just parts. Suppose we had taken a long time to do a methodical job, which means that the whole system wouldn’t get built and tested. We would’ve encountered each problem in a serial fashion. And then we would’ve found other problems once we were finished. That’s why people take ten years to do something. In our philosophy, we encountered problems in parallel because we built the whole thing at once. We knew we’d probably do things wrong. We hoped they’d have minimal effect.”
Turned out it was good that problems popped up so fast. A major energy provider in Florida called to do business. The utility company wanted to test some units at its headquarters, which meant that the solar trees had to withstand hurricane-force wind. “Our large unit, as it was, could never survive that,” Clemens says. “But we remembered that four-mirror unit we built for some early tests. Storms never budged that thing. We decided that for the next six months, that’s our product. And that’s what we’ll ship to Florida.”
But building a smaller solar tree would solve only part of the wind problem and none of the other issues. And building smaller units would mean producing less energy per tree, which could be a big blow to MegaWatt’s claim of providing energy at a cost cheaper than coal.
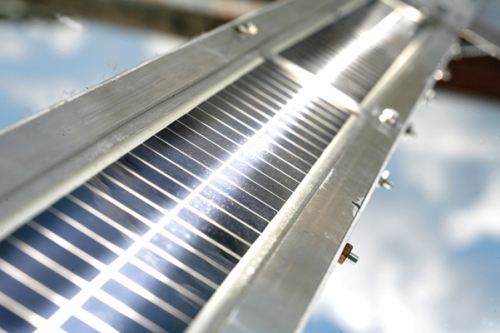
Photo by Coke Whitworth. ©2009 Endeavors magazine.
Small silicon cells absorb a band of concentrated sunlight. This solar receiver uses much less silicon than conventional rooftop panels while producing the same amount of energy.
Click to read photo caption. Photo by Coke Whitworth. ©2009 Endeavors magazine.
In the original design, the Dibond mirrors were part of the metal truss. Clemens and Evans knew that if the truss bent, then the mirrors would also bend. They just didn’t realize that this would mess up the band of light so much. “So we had to go back to a concept used in building major telescopes,” Evans says. “What’s called a kinematic mount.” They framed the mirrors individually and attached them to the truss with special mounting brackets. This way, when the truss bent, the mirrors didn’t. This new design is patent-pending.
Next, they scrapped the four-foot-long solar receiver. Instead, each solar collector would have two separate receivers right next to each other. No flexible joints. This was a sturdier design and produced the same amount of power.
Joey DeSena, another former UNC physics major, found a better encapsulant to protect the solar cells from the elements, and he helped redesign the aluminum plate that housed the silicon cells.
The company still couldn’t afford a new environmental chamber to test DeSena’s sealant, so Evans searched for a used chamber and found one on eBay for twelve hundred dollars. It didn’t work, but with help from a couple of electricians MegaWatt had hired, Clemens fixed the old, olive-drab contraption. The environmental tests were successful.
Third, the wind. The smaller units would survive hurricanes, but very strong gusts could still blow the mirrors off track. The sensors and tracking algorithm would eventually find the sun, but both were too slow. Clemens knew that he could’ve bought an expensive piece of technology that would actually read the position of each axis in the drive unit and then tell the mirrors where to move to find the sun. “But we needed a five-dollar solution,” he says.
During a board meeting, Clemens had an idea. “I saw one of our guys pushing his computer mouse,” he says. “And I thought, ‘Now that thing knows where it is. How can my tracker be stupider than that mouse?’”
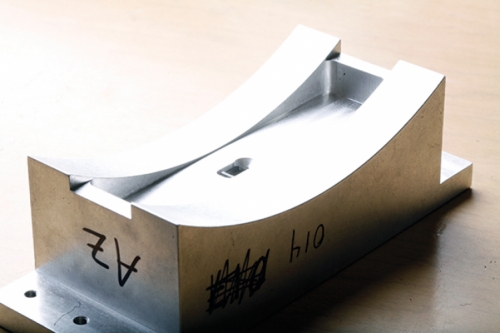
Photo by Coke Whitworth. ©2009 Endeavors magazine.
Clemens invented this optical navigation system to help each collector track the sun.
Click to read photo caption. Photo by Coke Whitworth. ©2009 Endeavors magazine.
After the meeting, Clemens took apart a mouse and attached its sensors to the drive unit’s stationary metal post. The sensor read how the axle was moving in relation to the metal post, just as a mouse arrow knows where it is on your computer screen. In MegaWatt’s shop, Clemens led the team to attach these mice — what the company is calling the optical navigation system — to the smaller units. He’s still tweaking the design, but the system helps the solar trees track the sun better than ever before.
These mouse sensors have two other advantages. When you lift a mouse off your desk, the sensor goes blind and stops working. So Clemens drilled holes in both axles. When the mouse sensors come to the holes at the end of the day, they go blind and realize that their tasks are done. Then, thanks to code that Taylor’s team wrote, the axles move back to their dawn positions.
The invention did what Clemens needed. The double-axis drive knew exactly where the sun was, and if the mirrors were blown off course the mouse sensors would find the sun again within thirty seconds.
All the problems from the Caswell plant were solved. Only one issue remained.
The four-mirror unit produced 750 watts of electricity instead of 3,000, which is how much a sixteen-mirror unit produces. When Clemens and the group crunched the numbers, they saw that the metal pole and drive unit would cost too much to make their power plants competitive with coal plants. They needed something even cheaper than metal but just as strong.
Clemens found something stronger: concrete. MegaWatt contracted with a company in Siler City, North Carolina, that could make precast concrete posts and platforms that weigh 5,550 pounds each and are as cheap as, well, cement. The cost of the solar trees dropped way down.
In April of 2009, MegaWatt Solar planted six newly designed units in the company’s back lot. And for weeks, the units tracked the sun better than ever before, though still not perfectly. They withstood strong winds and generated power.
The final step was getting that energy onto the grid.
All along, MegaWatt Solar had been working with NC State’s engineering department and CREE, Inc. — an NC State spin-off — to develop an inverter.
Evans says that inverters are well-known weak links in solar and wind technology because they tend to burn out after ten years. “And if you have to install a thousand inverters, and a few burn out each day, then that’s not a good thing.”
MegaWatt is now testing the new CREE inverters in Hillsborough and planning to ship six solar trees to the Florida utility company. The pilot plant is designed to last fifty years. Over that span, the average price of the energy it produces is estimated to be cheaper than coal, oil, natural gas, and nuclear energy. Much cheaper.
MegaWatt Solar is now in discussions with that same power company to produce 20 megawatts of power. That’s 26,400 four-mirror solar trees. The Piedmont power co-op in Caswell County expects to produce 50,000 watts with the 16-mirror units that MegaWatt Solar reengineered for redeployment by the end of 2009. Piedmont also wants an additional one megawatt of power — 1,320 four-panel trees. And as Endeavors went to press, MegaWatt Solar was negotiating with another large utility company about a second project in North Carolina.
Despite these possibilities and MegaWatt’s many innovations, the company has been affected by the recession just like many other start-ups. The original Norwegian investors — Scatec and iEnergies — had agreed to fund MegaWatt for two years. Those two years are up. MegaWatt found potential investors, but not that coveted lead investor.
In the summer of 2009, though, the founders struck a deal with iEnergies to keep MegaWatt chugging along. The Norwegian company stepped up to take majority ownership of MegaWatt Solar. Clemens, Evans, Taylor, and Gregory remain significant minority owners. In turn, the Norwegians injected new capital into MegaWatt Solar, which can now continue tweaking its new design while negotiating with utility companies. Gregory stepped down as MegaWatt’s chief executive and returned his focus to his “smart grid” company, PSi. Mark Conroy, who has been part of the iEnergies team in the United States, took over as CEO.
From MegaWatt’s inception, Gregory says, its founders knew that the time would come to bring in “big company” management to take MegaWatt to commercial success. If all goes well, MegaWatt will soon become a revenue-generating, profitable company.
“There is no chance this is going away,” Clemens says.
Early in 2009, the U.S. Department of Energy said that solar energy will have to grow at a rate of 26 percent each year until 2025 to keep up with energy demand and replace what the nation will be losing as oil and natural gas production peak and then sink into permanent decline. No energy source has ever grown so fast, according to Evans. Still, solar will have to be one of several alternatives to fossil fuels and traditional nuclear energy.
“We’re not so outlandish as to think that what we’ve developed will solve the energy crisis,” Evans says. “We just decided that if you’ve got the right training and if you’re at an institution that owes a debt to the public, wouldn’t you be remiss if you didn’t try to contribute to a solution? How much of a contribution this will be remains to be seen. There will be other competing solar and wind technologies. But we don’t worry about them because the market is so huge. We’ve just been competing with ourselves to get this right.”